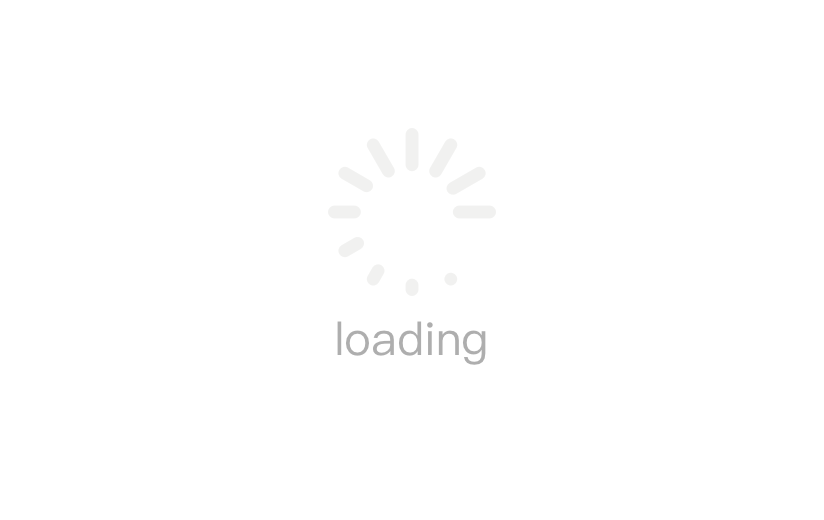
Лазерная резка является едва ли не самой передовой технологией резки в мире. Он способен резать как металлические, так и неметаллические материалы. Независимо от того, работаете ли вы в автомобильной промышленности, машиностроении или производстве бытовой техники, вы часто можете увидеть следы лазерной резки. Лазерная резка сочетает в себе такие характеристики, как высокая точность изготовления, высокая гибкость, возможность резки неправильной формы и высокая эффективность. Он может решить проблемы, которые не могут решить традиционные методы. Сегодня мы поделимся с вами некоторыми базовыми знаниями о технологии лазерной резки.
Принцип работы лазерной резки.Лазерная резка оснащена лазерным генератором, который излучает лазерный луч высокой энергии. Затем лазерный луч фокусируется линзой и образует очень маленькое световое пятно высокой энергии. Сосредоточив световое пятно на соответствующих местах, материалы будут поглощать энергию лазерного излучения, а затем испаряться, плавиться, удаляться или достигать точки воспламенения. Затем вспомогательный воздух высокого давления (CO2, кислород, азот) сдует остатки отходов. Лазерная головка приводится в движение серводвигателем, который управляется программой, и перемещается по заранее заданному маршруту на материалах, чтобы вырезать заготовки различной формы.
Категории лазерных генераторов (лазерных источников)
Свет можно разделить на красный свет, оранжевый свет, желтый свет, зеленый свет и так далее. Он может поглощаться или отражаться предметами. Лазерный свет тоже свет. И лазерный свет с разной длиной волны имеет разные характеристики. Усиливающая среда лазерного генератора, которая превращает электричество в лазер, определяет длину волны, выходную мощность и область применения лазера. А среда усиления может быть в газообразном, жидком и твердом состоянии.
1. Наиболее типичным газовым лазером является CO2-лазер;
2. Наиболее типичный твердотельный лазер включает в себя волоконный лазер, YAG-лазер, лазерный диод и рубиновый лазер;
3. Лазер в жидком состоянии использует некоторые жидкости, такие как органический растворитель, в качестве рабочей среды для генерации лазерного излучения.
Разные материалы поглощают лазерный свет с разной длиной волны. Поэтому лазерный генератор необходимо тщательно выбирать. В автомобильной промышленности наиболее часто используемым лазером является волоконный лазер.
Режимы работы лазерного источникаЛазерный источник часто имеет 3 режима работы: непрерывный режим, режим модуляции и импульсный режим.
В непрерывном режиме выходная мощность лазера постоянна. Это делает тепло, поступающее в материалы, относительно равномерным, поэтому подходит для скоростной резки. Это может не только повысить работоспособность, но и ухудшить влияние зоны термического воздействия.
В режиме модуляции выходная мощность лазера равна функции скорости резки. Он может поддерживать тепло, поступающее в материалы, на относительно низком уровне, ограничивая мощность в каждой точке, чтобы избежать неровной режущей кромки. Поскольку его управление немного сложно, эффективность работы невысока, и его можно использовать только в течение короткого времени.
Импульсный режим можно разделить на нормальный импульсный режим, суперимпульсный режим и сверхинтенсивный импульсный режим. Но основные их отличия заключаются только в различиях интенсивности. Пользователи могут принять решение, исходя из особенностей материалов и точности конструкции.
Подводя итог, лазер часто работает в непрерывном режиме. Но чтобы получить оптимальное качество резки, для определенных видов материалов необходимо отрегулировать скорость подачи, например, ускорение, скорость резки и задержку при токарной обработке. Поэтому в непрерывном режиме недостаточно просто снизить мощность. Мощность лазера необходимо регулировать изменением импульса.
Настройка параметров лазерной резкиВ соответствии с различными требованиями к продукту необходимо постоянно корректировать параметры в различных условиях работы, чтобы получить наилучшие параметры. Номинальная точность позиционирования при лазерной резке может составлять до 0,08 мм, а точность повторного позиционирования может достигать 0,03 мм. Но в реальной ситуации минимальный допуск составляет ± 0,05 мм для апертуры и ± 0,2 мм для отверстия.
Разные материалы и разная толщина требуют разной энергии плавления. Следовательно, необходимая выходная мощность лазера различна. В производстве владельцам фабрик необходимо найти баланс между скоростью производства и качеством и выбрать подходящую выходную мощность и скорость резки. Таким образом, зона резки может иметь соответствующую энергию, и материалы могут плавиться очень эффективно.
Эффективность, с которой лазер превращает электричество в лазерную энергию, составляет около 30%-35%. Это означает, что при входной мощности около 4285 Вт ~ 5000 Вт выходная мощность составляет всего около 1500 Вт. Фактическая потребляемая мощность намного больше, чем номинальная выходная мощность. Кроме того, по закону сохранения энергии другая энергия превращается в тепло, поэтому необходимо добавить
промышленный охладитель воды.
S&A является надежным производителем чиллеров с 19-летним опытом работы в лазерной промышленности. Производимые ею промышленные чиллеры подходят для охлаждения самых разных лазеров. Волоконный лазер, CO2-лазер, УФ-лазер, сверхбыстрый лазер, лазерный диод, YAG-лазер и многие другие. Все из S&A Чиллеры сконструированы из проверенных временем компонентов, обеспечивающих безотказную работу, поэтому пользователи могут быть уверены в их использовании.
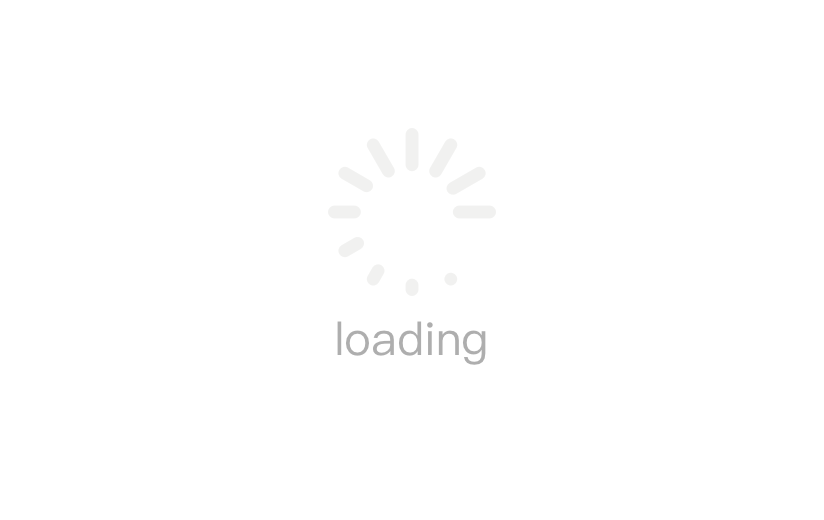